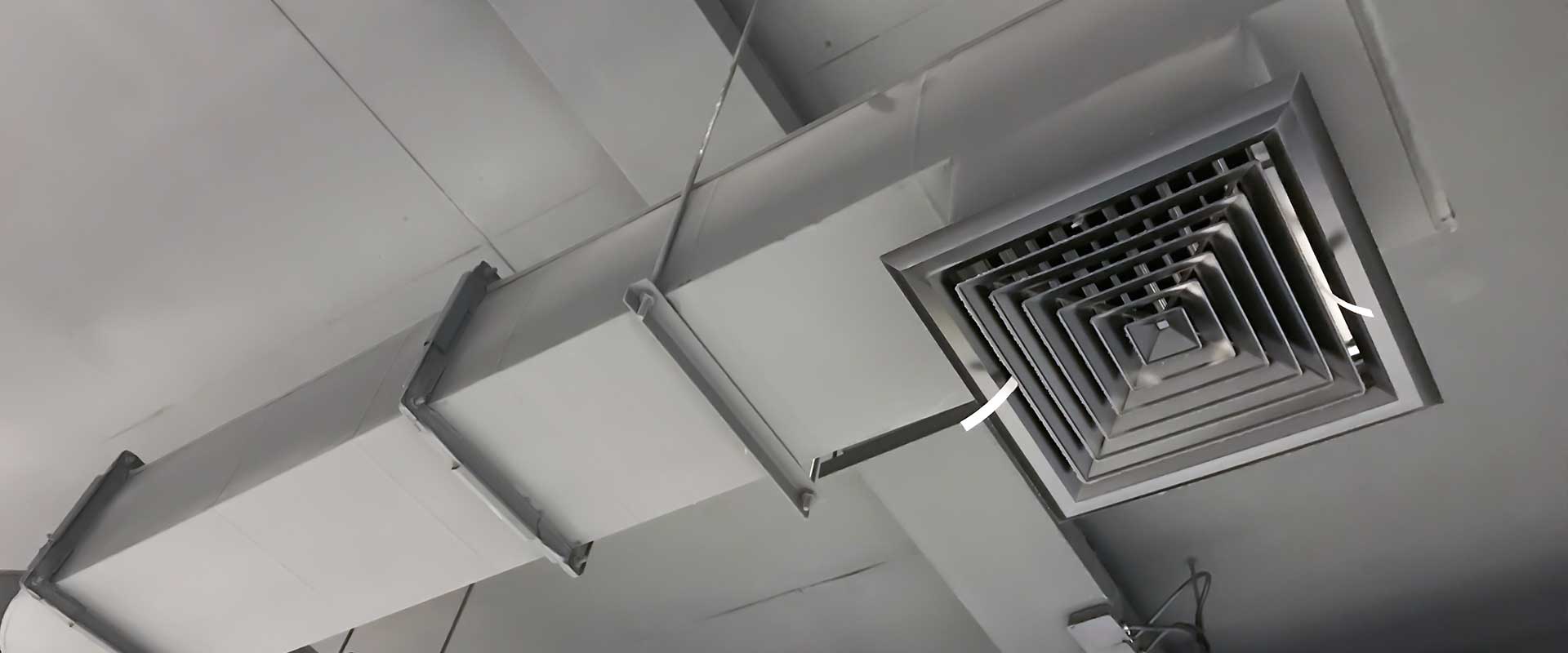
The TR19 Standard: A Comprehensive Overview
The TR19 is a standard that was defined by BESA, as a way to standardise duct and kitchen extract cleaning systems. Developed in 1988, it has become the standard to which most insurers and building engineering service sectors as the standard to match when performing ductwork cleaning operations.
To gain insight on why and how often ductwork and kitchen extract systems must be kept clean, check out our previous blog posts about Ductwork Cleaning and Kitchen Extract Cleaning.
What is BESA?
The Building Engineering Services Association is an association based in the UK. Established in 1904, it was previously known as the Heating and Ventilating Contractors’ Association (HVCA).
Structured as a membership association, BESA primarily focuses on supporting and serving their members active in the design, installation, commissioning, maintenance, control, and management of engineering systems and services in buildings.
20 years ago, they defined the TR19 standards, which has today become the go-to standard for performing ducts and kitchen extract system cleaning. Insurance companies only provide insurance to companies if they have a certificate of duct cleanliness that specifies that their ducts have been cleaned as per this standard.
What does the TR19 standard entail?
The TR19 is a comprehensive standard that details access mechanisms to the ductworks, inspection mechanisms, cleaning processes and post-cleaning verification methods. These have been detailed below:
Access Mechanisms
The inside of ductwork systems should be free of irregularities, which provide a conducive environment for accumulation of dust and grease. In addition to this, the standards also state that the system must contain access panels of sufficient number, quality and size so that the system can be cleaned and inspected regularly.
Although access to the ductwork is dependent upon a number of factors, like the location of the ductwork, building design, and more, a few things must be held in consideration. Access panels must be made of the same material as the ductwork. They should also include insulation, seals to prevent leaks, and quick release catches.
The placement of access panels is also important. It is highly recommended that the panels be located to the side or at the top of the ductwork, but at places where it’s not possible, panels on the underside of the ductwork should be properly fitted, and special care must be taken to make sure it does not leak.
Inspection mechanisms
Ductwork must be inspected in regular intervals to see if they require cleaning, and also to see accumulation of grease and dirt in the system does not exceed acceptable standards. Various tests, like the Wet Film Thickness Test (WFTT) for grease and other soft deposits and Deposit Thickness Test (DTT) for harder, carbonised deposits can be carried out to assess the system.
TR19 standards also specify that inspections must be carried out in regular intervals not exceeding 12 months. More frequent inspections are required for a precise measurement of the required cleaning interval. A specialist must carry out periodic inspections before and after cleaning the ductwork to assess whether the prescribed cleaning interval is alright, or if it needs adjustments.
The measurements of grease and dust deposits should be taken (where possible) at the following locations:
– Canopy/Extract plenum behind filters
– Duct 1 meter from canopy
– Duct 3 meters from canopy
– Duct midway between canopy and fan
– Duct upstream of fan
– Discharge duct downstream of fan
Cleaning processes
TR19 also specifies cleaning processes to be used when cleaning ductwork systems. Some of the necessary cleaning processes are:
– Hand Wipe: Manually wiping the surface of the ductwork system.
– Hand Scrape: Manually scraping heavy deposits off of ductwork surfaces.
– Chemicals: Using chemicals to soften or dissolve deposits, making it possible to scrape it.
– High Pressure Water Wash: Using high pressure water or vapour lance to dislodge or dissolve deposits.
– Blasting: Blasting contaminants off of duct and component surfaces, to be vacuumed afterwards.
Water or steam washing techniques may not be appropriate for ductwork systems situated above false ceilings or sensitive areas, unless they’ve been specifically designed for wet cleaning. Also, after using chemicals or liquid cleaning methods, care must be taken so that the fluids and residues are cleared from the system.
Apart from this, TR19 also recommends regular cleaning of the ductwork systems, depending upon their frequency of use. While multiple specialist inspections and cleanings must be done to gauge a more accurate cleaning frequency, the recommended cleaning intervals are given below.
– Heavy use (12-16 hours a day): 3 months
– Moderate use (6-12 hours a day): 6 months
– Light use (2-6 hours a day): 12 months
Post Cleaning Verification Methods
The primary method of assessing the cleanliness of the system post-clean is visual. The surfaces must be visibly clean and capable of meeting cleanliness standards. Further verification can be carried out through the use of WFTT and DTT, as mentioned in the inspection methods above. Deposits must not exceed .05 mm (50 μm) in thickness to pass the inspection.
After performing a verification, a Post Cleaning Verification Report must be provided that states the following details:
– The systems cleaned
– Pre-clean measurements
– Post-clean measurements
– Photographic records Â
– Additional works carried out Â
– COSHH data on any chemicals used
– Recommendations for future cleaning requirements
– Observations on the condition of the ductwork system
– A sketch or schematic of the system indicating access panel and testing locations and highlighting any uncleaned areas with a written explanation as to why the area could not be accessed/cleaned
This report can be used to provide proof of cleanliness to insurers and environmental agencies.
Ensure that your ductwork meets the TR19 standards
Choose innovatefm. Our teams are highly trained and meet the TR19 standards set by BESA. We also use the latest technologies and innovative methods to provide you with the highest quality, value-for-money service and provide you with a cleanliness report for insurance purposes.
Give us a call on (0161) 724 8999 (option 2) or email us at enquiries@innovatefm.co.uk​ for more information.